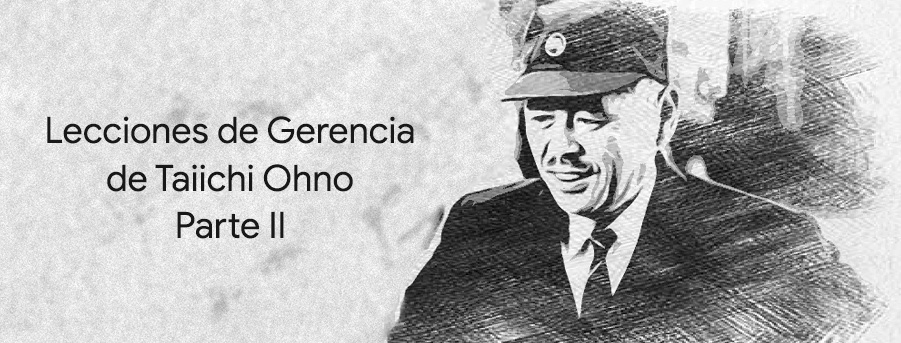
Esta es la continuación de las enseñanzas y lecciones del Dr. Taiichi Ohno, contenidas en el libro de Takehiko Harada – Management Lessons from Taiichi Ohno. A medida que vamos seleccionando partes del texto y las lecciones, me permite entender, mejor tal vez, el mindset del Dr. Ohno y la esencia del TPS. Me hace reflexionar sobre las enseñanzas de Eli Goldratt y la forma como con simplicidad podemos gestionar hasta las organizaciones y los flujos más complejos.
Lección 3: “Usted necesita en la línea solo las piezas para el automóvil que está ensamblando ahora”
“El significado obvio es conservar solo lo que se necesita en este momento, pero la otra razón para esto es liberar a los trabajadores de la difícil tarea de elegir la pieza correcta y, en cambio, hacer que se concentren en el trabajo de valor agregado”
“De la misma manera, el taller de máquinas equipó un juego de piezas para el motor, la transmisión y el chasis en caja que llamamos paleta”.
Enseñanza de Ohno
Si hace el trabajo lo más simple posible, tendrá menos errores y no tendrá que decir “obedezcan, obedezcan” porque la gente obedecerá las reglas. Además, si es simple, nacerá un método para tener menos inventario “.
Lección 4: “La construcción de lotes frena el crecimiento de sus operaciones (no combine Kanbans y cree un grupo de ellos)”
“Ohno: ¿Cómo es que tienes tres Kanbans iguales seguidos?
Nosotros: Producimos en lotes. Una vez que obtenemos tres kanbans, los juntamos y hacemos las partes.
Ohno: ¿Por qué no los haces en secuencia que llegan cuando recibes un kanban?
Nosotros: Se tarda una hora en cambiar la máquina cortadora de engranajes.
Ohno: ¿Cuánto tiempo llevas haciendo esto?
Nosotros: Durante mucho tiempo, señor.
Ohno: Mucho tiempo. Comprendo. De acuerdo, de ahora en adelante, debes hacer los engranajes en la misma secuencia en la que recibes los kanbans”.
“Lo que quiso decir fue que teníamos que hacer un cambio de una hora en la máquina cada vez que teníamos que fabricar un nuevo tipo de engranaje. El hecho de que Ohno dijera “Haz esto” no significa que nuestro tiempo de cambio de una hora se haya reducido. Además, vendría todos los días, por lo que no había forma de engañarlo. Pasábamos más tiempo cambiando la máquina que fabricando piezas, por lo que empezamos a encontrar escasez en casi todas las piezas. Cuando apareció la persona gestora del flujo corriente abajo, se trataba de poner los kanbans en la casilla de “faltante”. Ohno lo detuvo y le pidió que llamara al supervisor del taller de máquinas. “No pongas los kanbans en una caja. Debes informar al supervisor. Entrégale los kanbans en la mano. Hágale saber que hay un faltante de piezas y usted se quedará aquí hasta que las piezas estén hechas. Ir a casa con las manos vacías no tiene sentido, ¿verdad?”
“Él acabando de llegar, pregunta, y ¿estás haciendo las partes en la misma secuencia que cuando recibes los kanbans? ¿Verdad?”
“Alguien finalmente dijo que tal vez Ohno estaba mostrándonos que necesitábamos reducir el tiempo de cambio en la máquina cortadora de engranajes”
“La máquina cortadora de engranajes era uno de esos procesos que tenía uno de los tiempos de cambio más largos. Por eso, estaba fabricando piezas en lotes, y ese método había funcionado bien. Esto es algo de lo que realmente me arrepiento. Era cierto que reducir el tiempo de cambio iba a ser difícil, pero el error fue que habíamos aceptado el largo tiempo de cambio como una realidad que no se podía cambiar. Estábamos equivocados”.
Las palabras de Ohno fueron claras – “La producción en lotes frena el crecimiento de sus operaciones. No combine kanbans y cree un grupo de ellos. Produzca en la misma secuencia en la que reciben los kanbans”.
“Desafortunadamente, esta idea de agregar kanbans y luego comenzar a trabajar se ha vuelto bastante común. Incluso si se han reducido los tiempos de cambio, los tamaños de los lotes siguen siendo los mismos, solo que el tiempo ahorrado se utiliza ahora para una producción mayor. Entiendo que tenemos que ser competitivos en el mercado global y que cada área quiere lucir bien, pero recomendaría encarecidamente pasar de la eficiencia local a una eficiencia general, global en la que se reduzcan las paradas y el flujo general vaya tomando forma”.
“La ingeniería de producción y mecánica se trata de luchar contra las restricciones e interrupciones del flujo. Este incidente requiere que nunca me olvide que es una pelea, y una pelea que no es fácil “.
Conclusiones
La forma de mejorar la productividad y la calidad pasa por controlar el WIP. Si los trabajadores están recibiendo solo las piezas, que deben producir y ensamblar inmediatamente, porque son las que tienen ya un compromiso inmediato de entrega, hace que estén enfocados y hagan las cosas mucho mejor. El WIP elevado no solo contribuye a la mala multitarea, sino que desencadena en mala calidad, distracción, desgastes y tiempos de retrabajo y tiempos muertos.
Es refrescante aprender y leer que la preocupación por el flujo tiene una raíz común de cómo entendemos las prioridades en Teoría de Restricciones. El Enfoque debe partir por la restricción. Es la que generalmente controla, y dicta el flujo. Y por eso se requiere la sincronización. Tratar de ahorrar tiempos de arreglo o cambio en recursos que tienen capacidad suficiente es un espejismo cuando se piensa que reduce el costo. El conflicto existe y se genera por la convicción errada de que los arreglos tienen un costo. Esto solo es verdad cuando el recurso o maquinaria realmente incide sobre el flujo o es la restricción. La segunda alternativa es que ese recurso, está muy cerca en capacidad de la restricción, y más cambios producen un efecto de convertirlo en cuello de botella. Es por eso que los recursos que alimentan a la restricción deben ser siempre evaluados y entendidos a la luz de la capacidad que tienen de suplir y alimentar la producción de los recursos críticos en la secuencia que se requiere. Hacer lotes es la estrategia correcta cuando estamos en la restricción y tenemos limitaciones de capacidad. Un esfuerzo de SMED y de reducción de la variabilidad en este recurso puede resultar en mejorar el perfil de capacidad y eliminar la situación de posibles restricciones interactivas.
Siempre, siempre nuestra aproximación debe iniciar por seguir la demanda lo más fielmente posible. (Lo que Ohno en este caso insiste son los Kanbans que se reciben, y hacerlo en la secuencia y no agregarlos para agrandar un lote.) Las razones para dejar los lotes intactos es porque realmente hay una limitación técnica para reducirlos. Y aún así siempre hay una forma de retar las limitaciones técnicas.
Lo invitamos a leer este documento que registra un encuentro histórico: